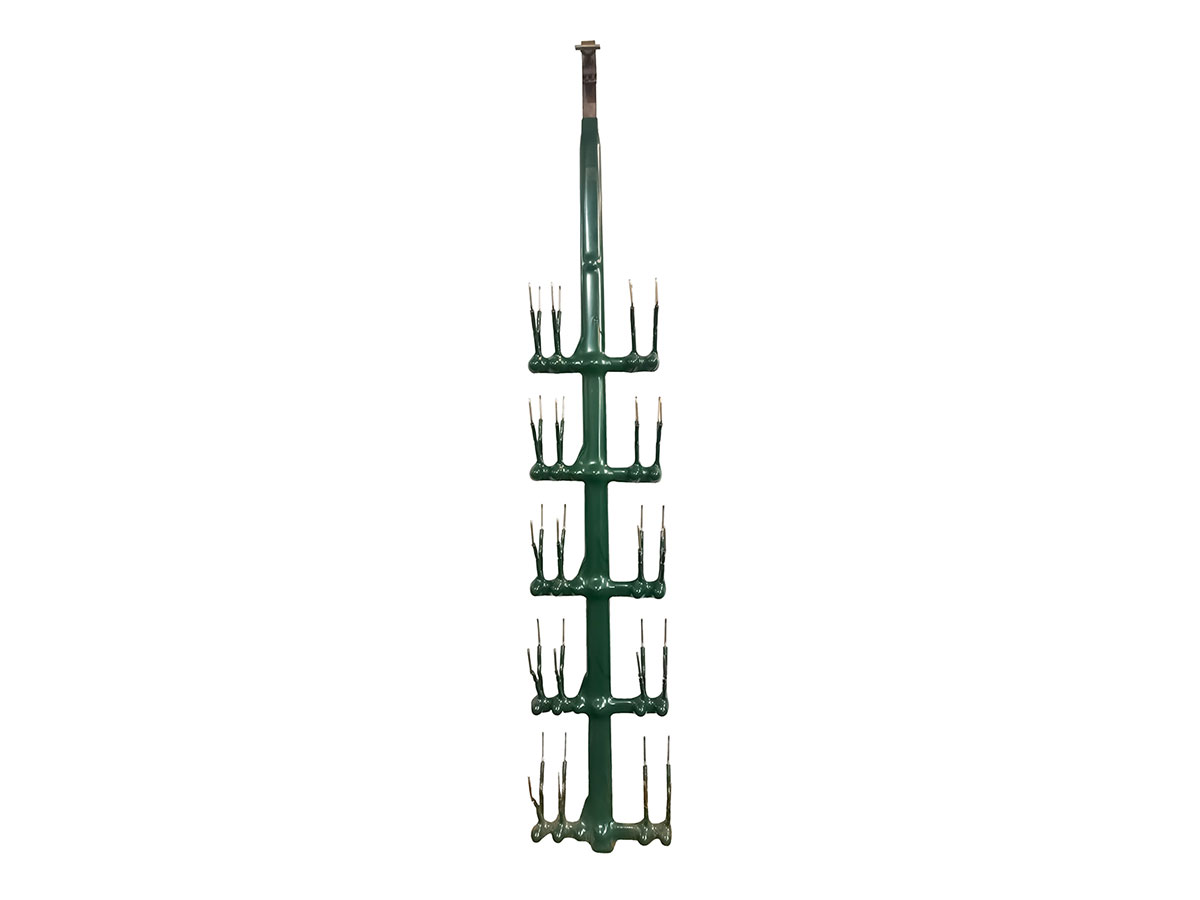
Electroplating Hanger
Hangers can be divided into two situations: one is a specialized hanging device designed and manufactured for mass production of parts; Another type is specialized hanging fixtures designed based on the complex geometric shape of the parts and special process requirements
Hangers are suitable for various parts and processes. The form and structure of electroplating hangers should be determined based on the geometric shape of the plated parts, the technical requirements of the coating, the process method, and the size of the equipment. For example, sheet-like plated parts may drift off between the upper and lower processes due to the resistance of the plating solution. When selecting hanging tools, the plated parts should be clamped or tied tightly with copper wire. If the plated part is heavy and has holes, a hook shaped hanging tool can be used.
(1) The loading weight of the hanging device is generally 3-6kg.
(2) The hook should have sufficient conductive area and its type should ensure good conductivity. Hangers and hooks should be cleaned regularly.
(3) When using, it is important to handle it with care and avoid damaging the insulation layer as much as possible. Otherwise, it will cause the hanging device to compete with the workpiece for power, resulting in localized failure or roughness of the workpiece, which will affect the quality of the coating.
(4) After using the hanging device, it should be cleaned thoroughly and stored properly for future use.
(5) After using the hanging device for a period of time, it is necessary to handle it in a timely manner and remove the coating on the hanging device to ensure good conductivity. Cracks in the insulation layer of the hanging device should be repaired or re insulated in a timely manner.
Chromium plating fixture: The chromium plating solution has strong oxidation ability, and the hanging material should be stable. Titanium or purple copper can be used as hanging tools. The conductive part of the fixture should have sufficient cross-sectional area and not generate heat. The fixture structure is connected by welding, and the conductive copper hook should be bent into a right angle shape. Fixtures and parts should be in contact with threads as much as possible. The anode and cathode of the chrome plated fixture in the inner hole must be isolated from electricity. Use insulating blocks (hard plastic sheets or organic glass) instead of protecting the cathode. The non working surface of the fixture should be insulated to reduce current consumption. The position where the parts are mounted should be the easiest for gas removal. Hangers should be as lightweight, simple, versatile, and easy to load and unload as much as possible, while ensuring their suitability.
When anodizing aluminum parts, aluminum and aluminum alloy hangers should be used. Hangers should have elasticity to clamp the parts and prevent the formation of non-conductive oxide films due to loose contact, which may affect the continuation of anodizing.
The structure of hangers is generally relatively simple, consisting of five parts: hooks, lifting rods, main rods, support rods, and hooks.
The hook is the connection structure between the hanging device and the pole, which transfers current to the hanging device and parts during electroplating. Therefore, it must be made of materials with good conductivity. The hook and pole should maintain a large contact surface and good contact state to ensure smooth current flow. Its cross-sectional area is equivalent to the cross-sectional area of the same material as the main pole of the hanging device. The hook needs to bear the full weight of the hanging device and plated parts, so it requires sufficient mechanical strength. The hook and the main pole are usually made of the same material, and the two can be made as a whole or separately. They can be connected to the pole by brazing or other methods and hanging tools. Hangers made of steel or aluminum alloys, hooks are generally made of copper, and connection methods can be riveting and welding. Its size should be designed according to the diameter of the cathode rod, making the hanging device easy to operate during suspension and removal.
The lifting rod is located at the upper part of the main pole and perpendicular to it, and is connected to the main pole by welding. When the hanging tool is suspended in the plating tank, the position of the lifting rod should be about 80 mm higher than the liquid level.